Selecting the right Programmable Logic Controller (PLC) is a critical decision for any industrial automation system. The right PLC ensures efficiency, scalability, and reliability in your operations. In this guide, we’ll walk you through the key factors to consider when choosing a PLC, helping you make an informed decision that aligns with your current and future needs.
1. System Compatibility: Seamless Integration is Key
When choosing a new PLC, compatibility with your existing systems is paramount. Ask yourself:
- Can the PLC communicate effectively with your current hardware and software?
- Does it support the communication protocols used in your facility (e.g., Ethernet, Modbus, Profibus)?
- Is it compatible with devices like HMIs (Human-Machine Interfaces), VFDs (Variable Frequency Drives), and other control systems?
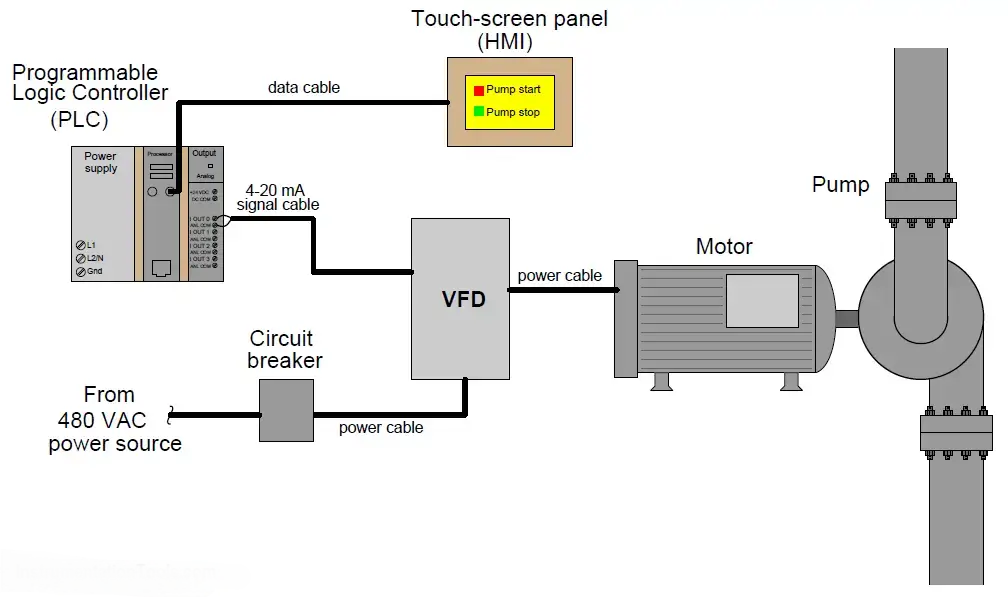
Pro Tip: Always consider future expansions. Choose a PLC that is scalable and can adapt to technological advancements.
2. Hardware Specifications: The Backbone of Your PLC
The hardware components of a PLC determine its performance and suitability for your application. Here’s what to evaluate:
Central Processing Unit (CPU)
- The CPU is the brain of the PLC, responsible for executing control instructions and processing data.
- Consider its speed (measured in MHz or GHz) and architecture (32-bit or 64-bit) to ensure it can handle complex tasks efficiently.
Memory Capacity
- PLC memory is divided into program memory (for control programs) and data memory (for process variables).
- Larger memory capacity is essential for handling complex operations and storing more data.
Communication Interfaces
- Evaluate the types and number of communication ports (Ethernet, RS-232/RS-485, USB) to ensure seamless connectivity with other devices and networks.
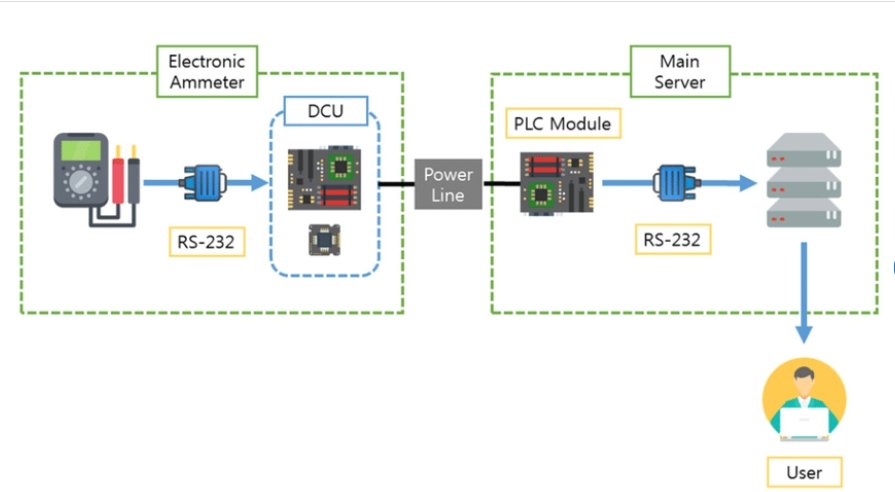
Input/Output (I/O) Ports
- I/O ports are critical for interfacing with sensors and actuators. Consider the types of I/O ports required for your application:
- Analog I/O: For continuous signals like temperature or pressure.
- Digital I/O: For on/off states like switches or relays.
- High-Speed Counters (HSC): For precise counting in high-speed processes.
- Pulse Width Modulation (PWM): For controlling devices like servo motors.
3. Programming Language Options: Choose the Right Tool for the Job
PLCs support multiple programming languages, each suited for specific applications. Understanding these languages can help you optimize development time and system performance:
- Ladder Logic (LD): Ideal for simple control systems and users familiar with electrical relay logic.
- Instruction List (IL): A low-level, text-based language suitable for memory-constrained applications.
- Function Block Diagram (FBD): A graphical language effective for process control and complex mathematical operations.
- Structured Text (ST): A high-level language for complex algorithms and data processing.
- Sequential Function Charts (SFC): Best for sequential control processes and batch operations.
4. Software Capabilities: Enhancing Productivity and Ease of Use
Modern PLC software enhances productivity and ease of use. Key features to look for include:
- Online Editing: Modify programs in real-time without stopping operations.
- Simulation Modes: Test programs without physical hardware to validate logic and troubleshoot errors.
- Automatic Device Detection: Simplify setup by automatically recognizing connected devices.
- Find & Replace: Efficiently modify large programs.
- Cross-Referencing: Trace variables and elements for debugging and program flow analysis.
- Custom Function Block Libraries: Create reusable code blocks for consistency and efficiency.
- Diagnostic Tools: Monitor system performance and identify issues in real-time.
- Comprehensive Documentation: Detailed guides and examples for easier programming and maintenance.
- User-Friendly Interface: Intuitive navigation and design for improved productivity.
5. Power Supply and Voltage Compatibility
Ensure the PLC’s power supply and I/O voltage levels are compatible with your facility’s infrastructure:
- Supply Voltage: Common options include 24V/48V DC (for safety and reliability) and 120V AC (for larger systems).
- I/O Voltage: Match the PLC’s I/O voltage levels (e.g., 5V, 12V, 24V DC or 120V AC) with the connected devices.
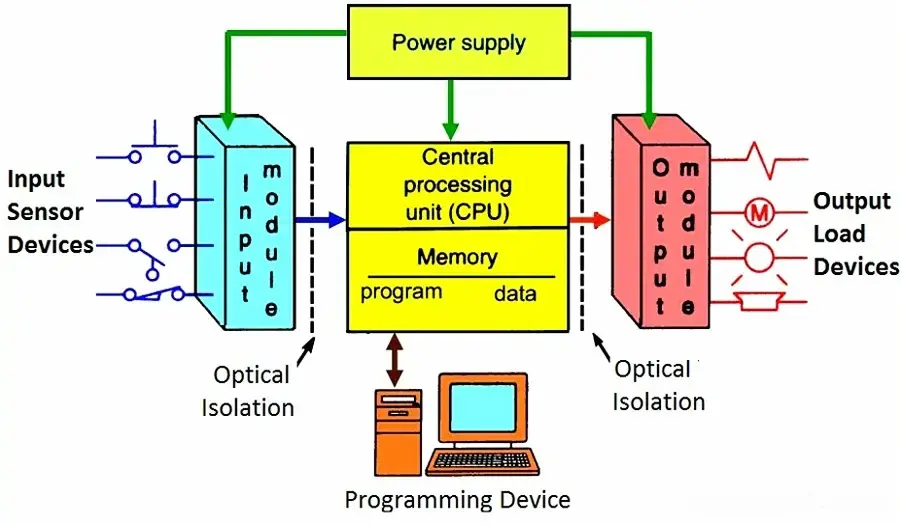
6. Scan Time and Processing Speed: Ensuring Real-Time Performance
Scan time—the time taken to complete one operational cycle—directly impacts the PLC’s responsiveness. Factors affecting scan time include:
- Control Program Complexity: More complex programs increase scan time.
- I/O Processing: Analog signals and high-speed counters require more processing time.
- Data Logging and Special Functions: Advanced features like PID control or motion control can lengthen scan time.
- Processor Speed: A faster CPU reduces scan time, improving real-time performance.
7. Environmental Durability: Withstanding Harsh Conditions
PLCs must withstand the operating environment’s challenges, including:
- Temperature: Ensure the PLC operates within the specified temperature range.
- Vibration: Choose ruggedized PLCs for high-vibration environments.
- Humidity and Dust: Select PLCs with high ingress protection (IP) ratings.
- Corrosive Atmospheres: Use PLCs designed for harsh conditions.
- Electromagnetic Interference (EMI): Ensure proper shielding and grounding.
- Explosive Atmospheres: Opt for PLCs certified for hazardous environments (e.g., ATEX).
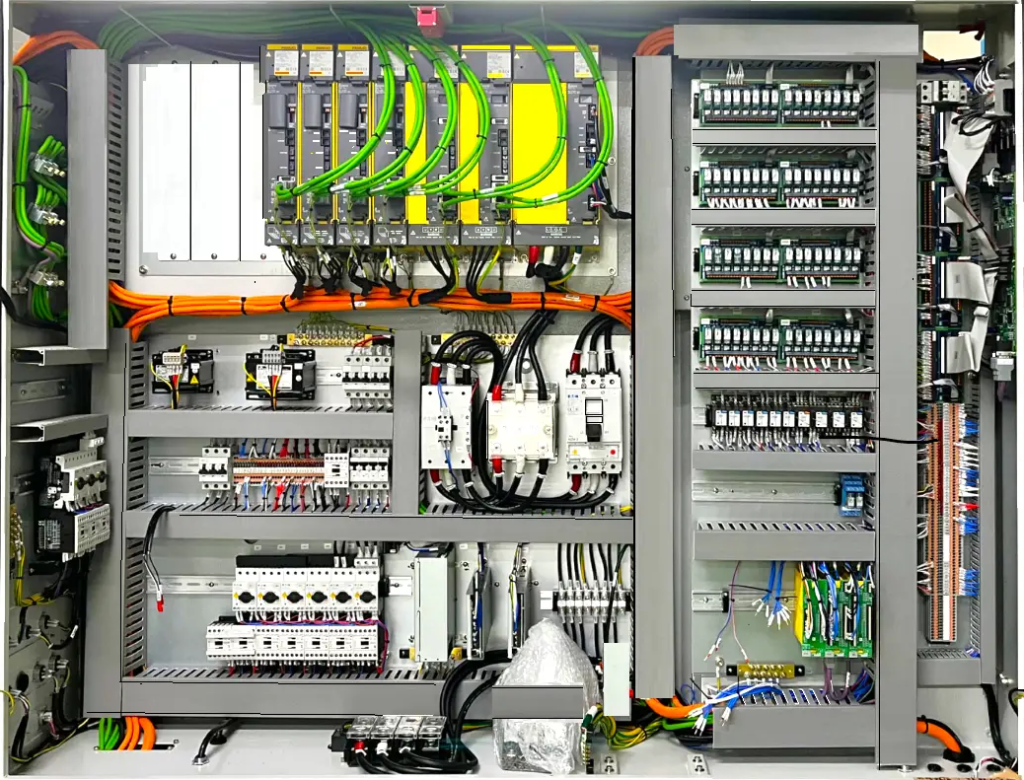
8. Industry Certifications: Ensuring Safety and Compliance
Certifications ensure the PLC meets safety, quality, and environmental standards. Key certifications include:
- UL (Underwriters Laboratories): Safety standards for North America.
- CE (Conformité Européenne): Compliance with EU health, safety, and environmental regulations.
- NEMA (National Electrical Manufacturers Association): Protection against dust, water, and corrosion.
- IP (Ingress Protection): Protection against solids and liquids.
- RoHS (Restriction of Hazardous Substances): Compliance with environmental safety standards.
- ATEX (Atmosphères Explosibles): Certification for explosive environments.
- FCC (Federal Communications Commission): Limits electromagnetic interference.
9. Physical Size and Installation: Fitting Your Space
The physical size of the PLC affects installation, scalability, and heat dissipation:
- Space Constraints: Compact PLCs are ideal for limited spaces.
- Scalability: Modular PLCs allow for expansion but require more space.
- Heat Dissipation: Larger PLCs dissipate heat more effectively.
- Installation and Maintenance: Ensure the PLC is accessible for wiring and maintenance.
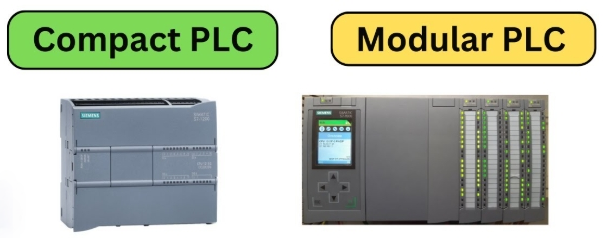
10. Technical Support and Resources: Ensuring Long-Term Success
Reliable support resources are essential for long-term success:
- Documentation: Comprehensive manuals and troubleshooting guides.
- Training and Education: Online tutorials, webinars, and hands-on training.
- Technical Support: Responsive customer service for troubleshooting and issue resolution.